LOD 350 Precast Structural Elements with Rebar
Client Profile :
The client is a well-established manufacturer in the precast concrete industry, with a strong focus on delivering customized structural components tailored to specific project requirements. Their expertise lies not only in the precision manufacturing of a wide range of precast concrete elements including columns, beams, wall panels, and slabs but also in providing technical support during the on-site assembly and installation processes.
By leveraging advanced casting techniques, standardised moulds, and rigorous quality control measures, the firm consistently meets the demands of large-scale infrastructure and building projects. Their hands-on involvement during the assembly phase ensures that each component integrates seamlessly into the overall structure, reducing on-site errors and enhancing construction speed.
Business Need :
As a U.S.-based manufacturer specialising in high-grade precast concrete components, Client aimed to improve efficiency and reduce costs through BIM implementation. Their key requirements were:
- BIM-Based Modeling & Tagging
- Model several box culverts and related precast components using BIM.
- Assign intelligent tags with key metadata (weight, dimensions, IDs) for each component.
- On-Site Erection Optimization
- Ensure erection teams have prior knowledge of component size and weight.
- Allow crane and lifting equipment to be pre-configured, reducing idle time.
- Goal: Achieve a 20–30% reduction in on-site delays due to lifting coordination.
- Mould Reuse Strategy
- Maximize the reuse of formwork/moulds across different concrete components.
- Goal: Reduce mould manufacturing costs by up to 25%.
- Cost & Quantity Control
- Generate a detailed and accurate Bill of Quantities (BOQ).
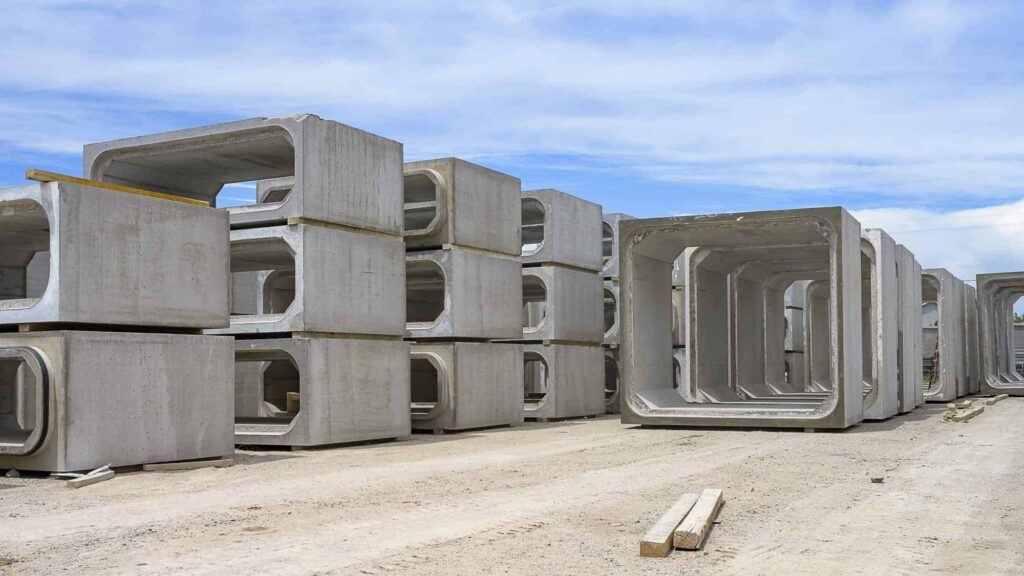
Challenges:
During the course of the project, the BIM Associates team identified several key challenges while analyzing the client’s requirements, workflow, and evolving timelines:
1. Precision in Precast Modeling
– As the project involved precast concrete structures, maintaining accurate gaps and tolerances between elements in the Revit model was critical. The design rules were highly stringent and required meticulous attention to detail.
2. Weight Limitations
– Each structural element, including embedded rebar, was not to exceed 25 ton. This required careful modeling and review to ensure compliance with lifting and transport constraints.
3. Lifting elements model accuracy
– Lifting bars had to be placed in perfect symmetry to prevent imbalanced loads, which could lead to structural damage or pose safety risks during erection.
4. Interdisciplinary Coordination
– Effective collaboration with other disciplines (e.g., MEP and architectural teams) added complexity to the modeling and coordination process, requiring full clash detection and resolution.
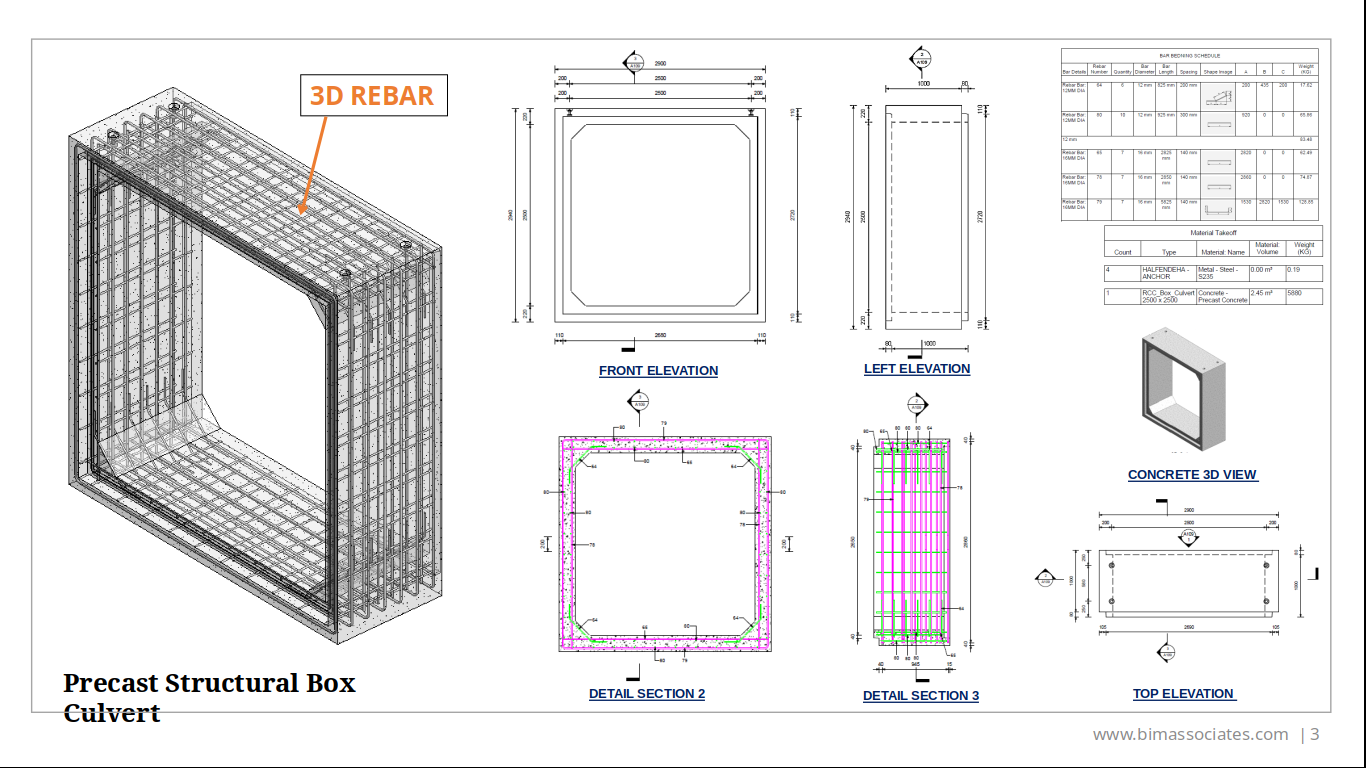
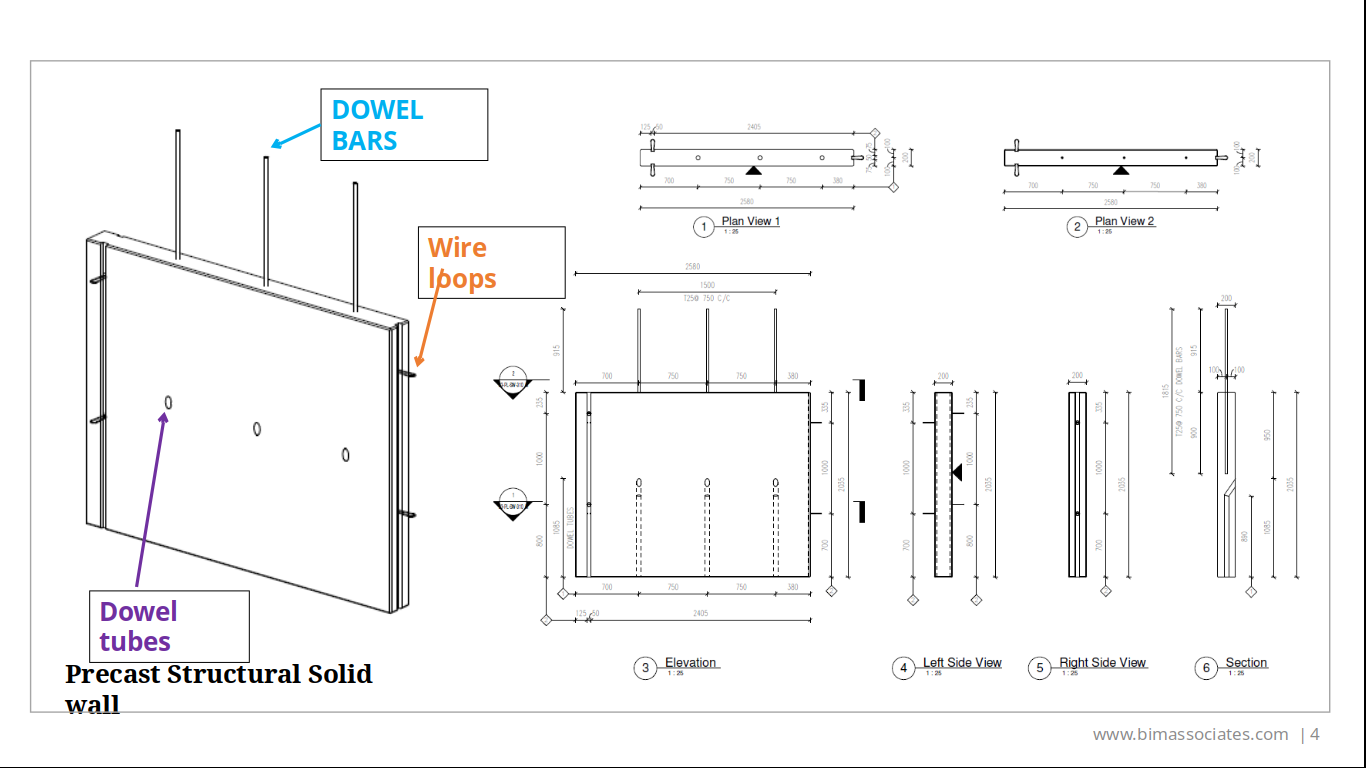
Solution :
To address these challenges, the BIM team at BIM ASSOCIATES implemented a structured and detail-oriented approach:
– Revit-Based Structural Modeling : A comprehensive 3D structural model was developed in Revit, incorporating predefined rules for spacing and tolerances between precast components.
– 3D Connection Detailing : All connection details were modeled directly within the Revit environment to eliminate ambiguity during fabrication and assembly.
– Component Identification & Tracking : Each precast element was assigned a unique ID, which was embedded into a corresponding QR code. These IDs were reflected in the erection floor plan, streamlining identification, transport, and on-site placement.
– Formwork Optimization : Sets of typical structural elements were reviewed with the client’s design team. This allowed the reuse of moulds for multiple components, based on the unique ID system. | Outcome : Significant savings in mould production costs and casting time.
– Weight Compliance Verification : Every element’s weight was calculated within Revit and verified by the client to ensure it remained under the 20-tonne threshold, enhancing safety and compliance.
– Clash Detection & Resolution : Full interdisciplinary clash detection was carried out, resolving all conflicts between structural, architectural, and MEP components before execution.
Approach :
Following the finalization of scope and deliverables in coordination with the client’s team, Our team adopted a structured approach as outlined below:
- Team of 3 resources with dedicated Project Lead, built a detailed Revit Structural model as per specification and norms given by client design team.
- Each elements was detailed and connections were added to the same in Revit model.
- After reinforcement detailing (rebar modeling) was completed, the team performed a thorough verification of element weights and checked for any clashes within rebar layouts or connections. These were reviewed and resolved in collaboration with the client’s structural design team
- Once this was done unique ID was given to each structural member, the same ID were also integrated into the erection plan to support efficient on-site assembly and tracking.
- Comprehensive clash detection and resolution were carried out across all disciplines, including architectural and MEP, ensuring seamless internal connections and enabling accurate quantity take-offs.
- A list of typical components was identified and submitted to the client, categorized by size and count, to facilitate optimized mould reuse and streamlined production planning.
- This coordinated modeling and review process significantly improved the client’s efficiency in manufacturing, transportation, and on-site erection of components. It also contributed to measurable savings in time and material, enhancing the overall return on investment (ROI) for the project
Workflow :
The below is a basic workflow for project. Please note fine details on the same are not shown here.
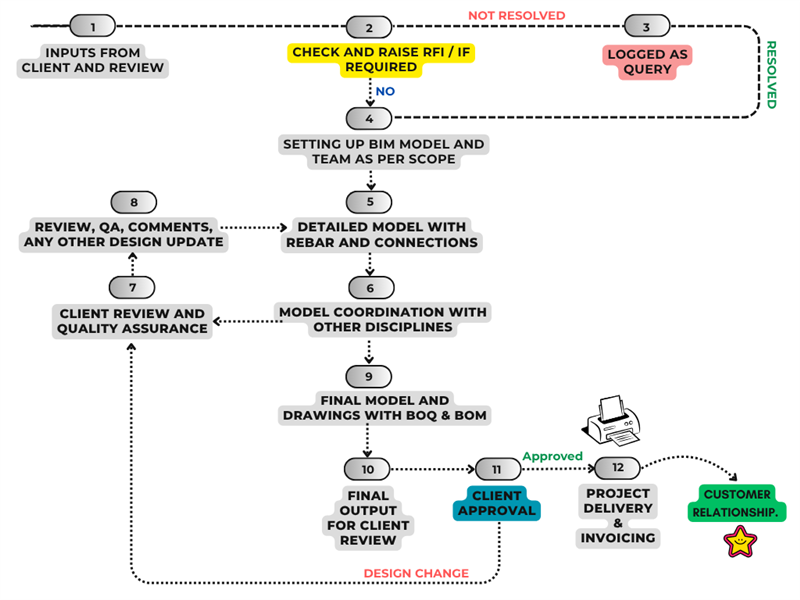
Software and Technology :
Autodesk Revit, AutoCAD, 3ds Max and Vray NXT.
BUSINESS IMPACT :
✓ Faster Construction & Cost Savings : Smart BIM modeling enabled precise procurement planning of high-strength materials , sequencing of modular formwork systems and quicker execution leading to significant reduction in overall project costs.
✓ Efficient Turnaround : BIM facilitated early quantity take-offs, cost estimation, and scheduling, helping us maintain budget accuracy and deliver the project within a compressed timeline.
✓ Proactive Risk Management through BIM Data Utilization : BIM’s centralized data environment helped in identifying design risks at early stage, tracked progress in real time, and enabled data-driven decision-making across all phases.
✓ Improved Site Coordination : With cloud-based BIM collaboration, teams on and off-site worked in sync. This minimized rework, enhanced real-time communication, and accelerated execution.
✓ Smart BIM & Clash Detection : the automated clash detection and design coordination done using BIM tools ensured early resolution of design conflicts, minimized rework, and kept construction aligned with the latest updates.
✓ Flexible Team Deployment: Adaptive working hours aligned with critical phases, improved overall responsiveness and delivery agility.
✓ Client Business Expansion through Value Addition : With optimized approach and enhanced deliverables, the client was able to offer a superior project package to their end customer. This not only boosted client satisfaction but also directly contributed to business expansion opportunities for our client in their target market.